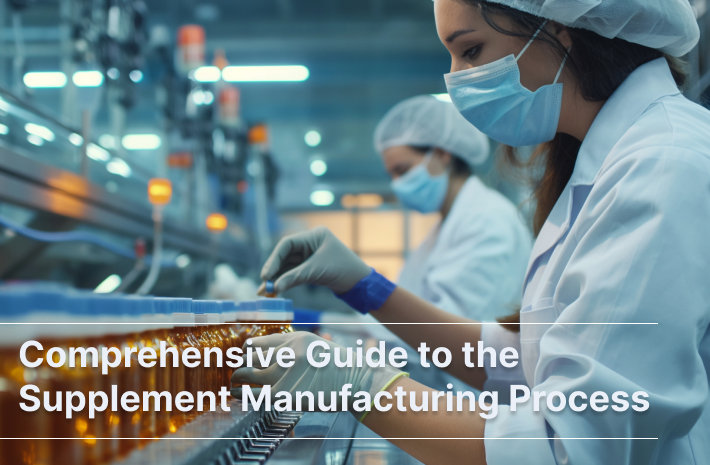
As health and wellness become top priorities for many, the popularity of dietary supplements has soared. This trend has driven consistent growth in the supplement industry, leading to a heightened demand for safe, effective, and high-quality products. This article explores the complexities of dietary supplement manufacturing and the challenges manufacturers encounter in maintaining rigorous quality and safety standards.
What are the Benefits and Uses of Dietary Supplements?
Dietary supplements are products crafted to enhance a person’s diet by providing essential nutrients like vitamins, minerals, herbs, amino acids, or enzymes. They come in various forms, including capsules, powders, and liquids, and are designed to support general health rather than treat or prevent diseases.
While dietary supplements can help address nutrient gaps and promote wellness, they don’t replace the benefits of a balanced diet. Because they are regulated differently from medications, it’s best to consult a healthcare provider before starting any supplement, especially for individuals with health conditions or unique dietary needs.
What Is the Supplement Manufacturing Process?
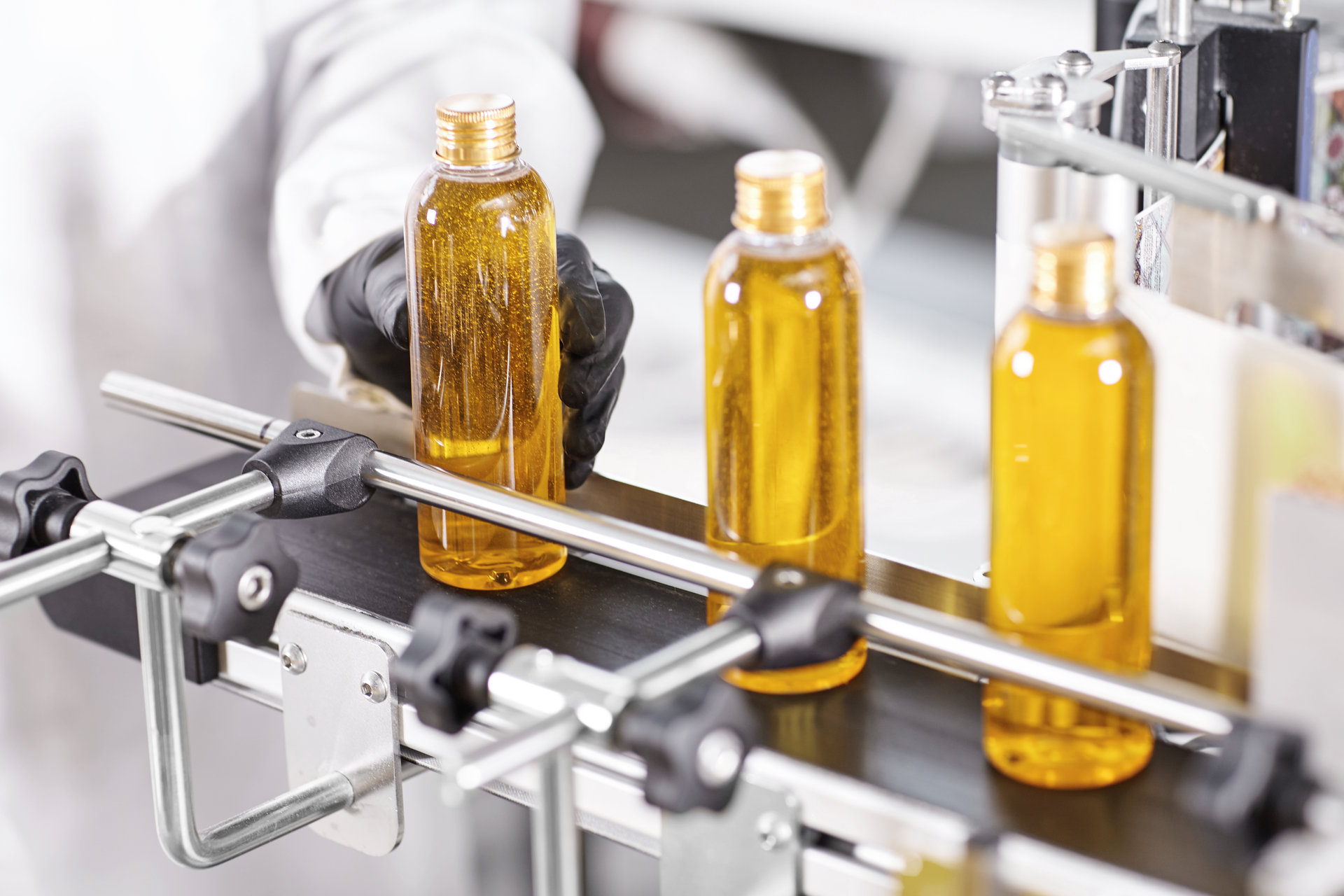
The supplement manufacturing process is a detailed and rigorous series of steps, each essential to ensuring that the final product is safe, effective, and high-quality. From the initial stages of formulation to final packaging, each phase requires precision and strict adherence to regulatory standards.
Below is an in-depth look at each step involved in producing supplements that meet industry requirements and consumer expectations.
Step 1: Developing the Supplement Formula
The supplement formulation process begins with a purpose-driven design that considers the specific wellness goals the supplement will support, which could range from immune support to cognitive enhancement. This involves selecting bioavailable, research-backed ingredients in precise dosages to optimize effectiveness.
Also, manufacturers often include unique or specialized ingredients to create a product that stands out in the market and addresses specific health needs. Every aspect of the formula is meticulously balanced to ensure that the final product meets both functional and safety standards.
Step 2: Selecting and Sourcing Raw Materials
The quality of raw materials is crucial to the effectiveness and safety of the final product. To achieve this, manufacturers carefully source ingredients from reliable, often global suppliers who are known for high standards.
Suppliers undergo a verification process where manufacturers assess their capacity to meet industry expectations for quality and safety. This step ensures that each supplement contains high-quality ingredients that support its intended effects.
Step 3: Pricing and Cost Estimation
Once the formula and raw materials are defined, manufacturers calculate costs to establish a competitive and profitable price. This involves evaluating every expense, from raw materials to packaging, and making necessary adjustments to align with the budget.
The goal is to balance cost with quality so the supplement can remain competitive without compromising efficacy. After finalizing costs, a quote is provided to the client, ensuring transparency and agreement on expenses.
Step 4: Purchasing Order and Supply Chain Coordination
After the client approves the pricing and costs, a purchase order is submitted to initiate the manufacturing process. This step signifies a commitment to move forward with production.
The manufacturer coordinates closely with suppliers to arrange timely shipments of all materials, thereby reducing potential delays and optimizing lead times for production. This coordination is essential for maintaining efficiency and meeting manufacturing timelines.
Step 5: Raw Materials Testing and Quarantining
Upon arrival, raw materials are quarantined and subjected to thorough testing to verify their quality and authenticity. This step involves screening for contaminants and verifying each ingredient’s potency and purity.
Materials that pass all tests are released for production, while those that fail are rejected. Testing at this stage ensures that only the best ingredients are used, reinforcing the product’s safety and effectiveness.
Step 6: Bench Work
Benchwork is the hands-on experimentation phase, where small samples of the formula are created in a lab setting. This allows the team to assess the formula’s texture, consistency, and dissolution rate. During this phase, lab technicians make adjustments based on real-world observations, ensuring that the product will function as intended once scaled up.
Step 7. Pilot Batch
The pilot batch stage involves producing a small batch of the supplement using production-level equipment. This step serves as a bridge between lab-scale and full-scale manufacturing, helping to identify any unforeseen issues in mixing, filling, or packaging before the full production run. It’s a critical stage to ensure consistency, quality, and reliability in large batches.
Step 8. Full-Scale Manufacturing
Once the pilot batch meets all quality standards, the product moves to full-scale manufacturing. Each supplement is produced in large quantities, utilizing production equipment that adheres to strict industry guidelines. This step involves continuous monitoring to ensure the manufacturing process aligns with the specified formula and safety regulations.
Step 9: Quality Control and Assurance
Quality control and assurance processes are integral to ensuring that every supplement adheres to established specifications. Each production step undergoes verification, which includes compliance testing to meet regulatory standards.
These tests confirm the integrity and accuracy of the product, ensuring it contains the ingredients stated on the label in the right dosages. Detailed records of each batch provide traceability and proof of compliance, guaranteeing that the product is safe and effective for consumers.
Step 10: Final Product Testing and Packaging
After quality control checks, the final products are subjected to comprehensive testing to confirm their effectiveness and compliance with regulations. Once tested, the supplements are packaged in clean, controlled environments to prevent contamination and preserve product integrity. Packaging is designed not only for safety but also to communicate product information clearly to consumers.
Step 11. Product Storage and Delivery
The last step involves storing the finished products in a controlled environment until they are ready for distribution. Proper storage conditions are essential to maintain product quality. Once ready for shipment, the supplements are distributed to retailers or directly to consumers, ensuring they reach the market efficiently.
This step-by-step process is designed to ensure that every supplement meets the highest standards, from formulation to final packaging, producing a product consumers can trust.
What is the FDA Regulation for Supplement Manufacturing
Supplement manufacturing is regulated primarily by the Dietary Supplement Health and Education Act (DSHEA) of 1994, which gives the FDA the authority to set Good Manufacturing Practices (GMPs) for dietary supplements. These regulations are crucial for ensuring that supplements are safe and of high quality. While the FDA doesn’t approve supplements before they hit the market, they monitor companies to ensure they comply with safety and labeling standards. If a product is misleadingly advertised, the Federal Trade Commission (FTC) can step in to enforce truthful marketing. Additionally, manufacturers must avoid making health claims that imply their products can treat or prevent diseases, as this would classify them as unapproved drugs. By following GMP guidelines, manufacturers can create reliable supplements that consumers can trust.
Emerging Trends in Dietary Supplement Manufacturing
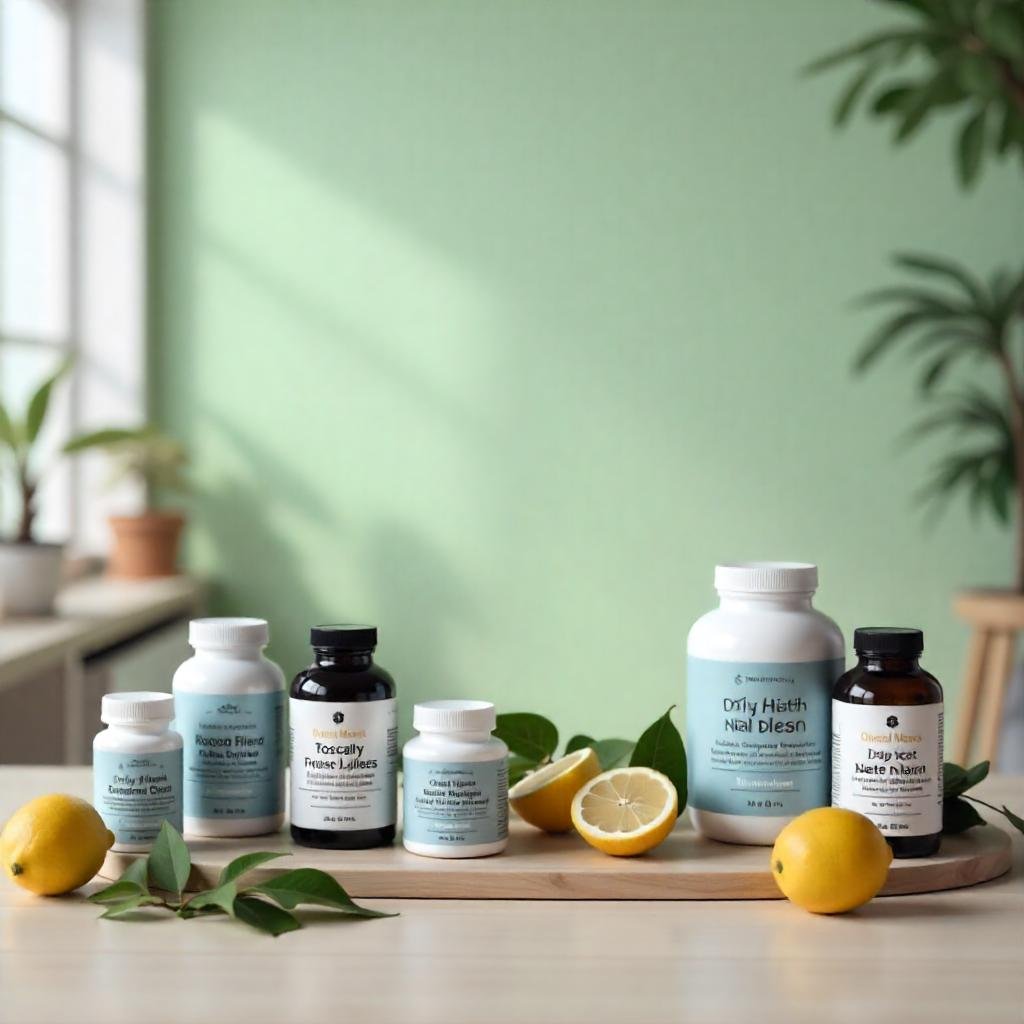
The dietary supplement manufacturing sector is experiencing significant transformation, driven by scientific progress and changing consumer demands. A major trend is the rise of personalized nutrition, with an increasing number of consumers looking for supplements tailored to their specific health needs.
In the U.S., the market for personalized nutrition and dietary supplements is expected to reach $4.55 billion by 2023, with a projected compound annual growth rate (CAGR) of 16.28% from 2024 to 2030. Moreover, innovative delivery formats, such as gummies and drink mixes, are gaining traction, with forecasts indicating that this market will grow to $48.5 billion by 2028.
Sustainability is another crucial trend, with 66% of consumers indicating they prefer products from brands that prioritize eco-friendly practices. This shift is pushing manufacturers to adopt greener processes to reduce their environmental footprint. The market is also seeing impressive growth in specific areas; for instance, collagen supplements are projected to grow at a CAGR of 5.3% from 2024 to 2030, while immune health supplements are anticipated to reach $130.4 billion by 2030.
Advancements in manufacturing technologies, such as automation and 3D printing, are enhancing efficiency and quality control, enabling companies to meet increasing demand without compromising product integrity. Overall, the future of dietary supplement manufacturing will be characterized by innovation, personalization, sustainability, and a strong focus on quality.
Partnering for Success: Choose ATP-Bio for Your Supplement Manufacturing Needs
The supplement manufacturing process is a complex yet essential industry characterized by innovation, regulatory compliance, and evolving consumer demands. As trends like personalized nutrition and innovative delivery formats gain traction, it becomes increasingly vital to partner with a manufacturer that understands these shifts and can adapt accordingly.
ATP-Bio stands out as a trusted partner for supplement contract manufacturing, offering advanced technology and competitive pricing to help you succeed in this dynamic market. With a commitment to quality, our facilities are FDA and NSF GMP-certified, ensuring your products meet the highest standards of safety and efficacy. We provide flexible minimum order quantities and the capability to handle both large-scale and custom orders, making it easy for businesses of all sizes to collaborate with us.
For a seamless and efficient manufacturing experience, explore our supplement contract manufacturing services. Let ATP-Bio help you bring your innovative supplement ideas to life while ensuring the highest quality standards.
Related Articles You May Be Interested in:
- How Protein Powder is Made: Protein Powder Manufacturing Guide
- How to Find a Supplement Manufacturer: 5 Key Steps
- How to Promote Supplements: Top Marketing Strategies
- What Does Third-Party Tested Mean and Why Is It Important?
ATP-Bio also provides the services below: